
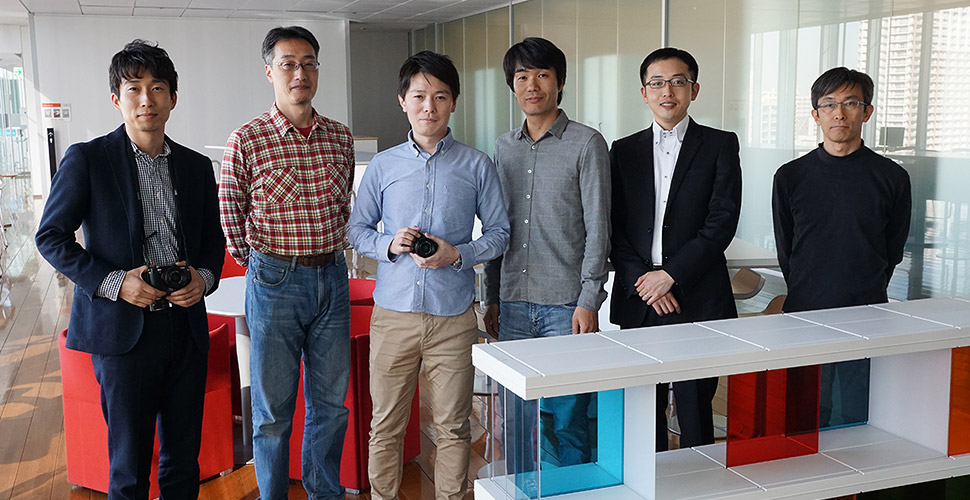
RX1 IDENTITY CONTINUES, INTEGRATED WITH NEW QUALITY AND SPEED
THE PINNACLE OF COMPACT PHOTOGRAPHY
RX1R II shows surprising evolution in response to user requests while carrying on the identity of the RX1 series. Now, the product development team shares important advances in the design of this impressive new Cyber-shot flagship.

MASASHI WAKATSUKI

SATOSHI MIYASHITA

TAKUJI YOSHIDA

AKIRA TAKEO

KAZUHITO TANEOKA

SHUNSUKE IKEO
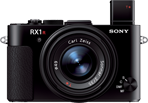
Aiming for natural depiction plus bold sensation using effective 42.4-megapixel image sensor and expanded ISO 102400 extended sensitivity
RX1R II is remarkable for its dramatically improved image quality, thanks to the renewed CMOS image sensor and image processing engine. Can you please explain about the development of these features?

We started discussing the concept of the new RX1 model with relevant team members a little while after the RX1R launch. Then we took sufficient time to determine the new camera structure and went ahead with design and evaluation. When the RX1 made its debut, there wasn't a compact camera with a 35mm full-frame sensor, and we were challenged to find a way to promote such a new camera in the market. On the other hand, the RX1R II has a precedent - that's the big difference. So we decided to listen to user feedback about the RX1 and RX1R and tried to reflect as many requests as possible, if this was technically manageable. Moreover, we wanted users to be surprised and pleased with results. How could we achieve these goals? How would these shape the new Cyber-shot flagship? We were busy thinking about new challenges.
The lens is unchanged from the first-generation RX1. Its "35mm F2" specification was decided in discussions before the RX1 debut, which concluded that a well-balanced lens is suitable for landscape shots, portraits, and casual snapshots. Because of this, we had no intention to change this spec. The lens has a significantly high performance potential, and we recognised that its resolving power was higher than the 24-megapixel full-frame RX1 image sensor. So rather than changing the lens, we combined it with a higher-pixel-count image sensor to achieve an even higher sense of resolution. Now the sensor provides effective 42.4 megapixels - dramatically increased from the previous sensor - while the image processing engine that handles enormous amounts of data was replaced by the new BIONZ X.

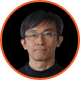
CMOS sensor development started with our desire for a major innovation to make the most of Sony's technological leadership in image sensors. This is the same sensor used in the α7R II - Sony's interchangeable-lens digital camera - but it was developed from the start for the RX1R II. Since a full-frame image sensor had to fit into the compact RX1 chassis, we had to cope with severe optical conditions including incidence angle setting. Taking these restrictions into account from the beginning, we proceeded with development to acquire necessary specifications and properties, working closely with Device Solutions Business Group which produces image sensor and Sony Semiconductor Corporation. Technologically speaking, the use of a backlit-type sensor - for the first time among 35mm sensors - enabled light to enter from a wider range of incidence angles while design optimisations included embedment of functional circuitry and heightened processing speed. Although each picture element is decreased in size due to the increased number of pixels, the backlit-type sensor allows increased light-gathering ability while the shape of micro lenses on the sensor surface is designed to pass light to photoreceptors without loss.
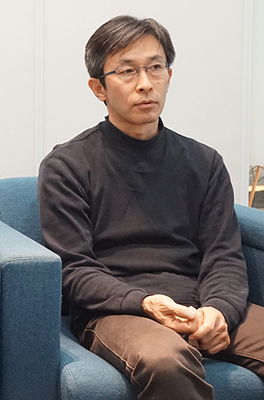
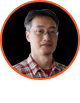
As the number of sensor pixels increases, the more power is required from the image processing engine. BIONZ X provides elevated ability to process image data as great as 42 megapixels - as well as handle highly sophisticated image processing. For example, one type of image processing is detail reproduction technology. In fact, any kind of image processing engine features technology to make pictures look sharper by emphasising object edges. Due to the nature of digital processing, these edges tend to look somewhat unnatural and even appear black or white. So we developed technology to produce a natural look in high-resolution images. Also, BIONZ X features a diffraction reduction processing function that compensates for blurred images caused by a small diaphragm aperture. Noise reduction technology has also been enhanced and enables capture of ever-higher image quality than was achieved through the previous BIONZ image processor, regardless of darkly or brightly lit shooting venues.
Though some characteristics are similar to α7R II, there are many unique tunings found only in the RX1R II. We were able to achieve imaging design suited to the lens, due to the strength of RX1R II lens-body integrated design. While we conducted numeric evaluations of colour and noise, we also considered the importance of using our visual sense to evaluate image quality. For example, we handle imaging design by criticising and judging picture quality, checking through printed output and monitor screens, and imagining environments where customers view the photos. We aim for natural images that are not artificially "crafted" and have a vividly realistic sensation - for example, a feeling of texture in shots of goods and an aerial feeling in landscape photos. We're proud the camera is so "completed" that it can achieve extremely natural depiction.
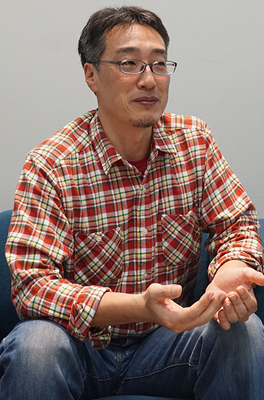

Achieving natural imaging involves difficulties in analogue as well as digital technologies. For example, some components generate electric and magnetic noise, affecting the image sensor. Such noise cannot be removed unless we optimise the design of the circuit board and placement of devices. Particularly because this camera is extremely small and has a number of severe technical limitations, minimising noise was one of the hardest challenges in this project, I believe.
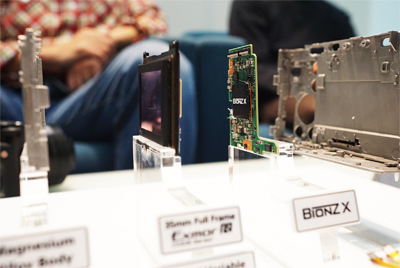
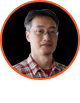
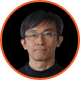
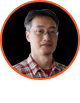
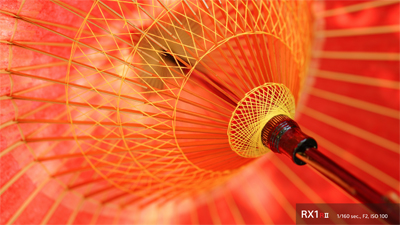

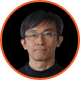
Yes, but it's not that easy to solve problems quickly. The image sensor receives light, converts it to electricity, and sends out signals. It handles multiple optical and electronic functions, and it's affected by electric noise from other parts. Since our customers now use digital cameras under very strict conditions, our job is getting tougher, but we can show our expertise through these challenges. We also put meticulous effort into installing the circuit board in the chassis, resulting in high quality that allows use at over ISO 100000 with confidence, we believe. The best feature of a camera with such a high pixel count is its ability to capture clean, natural images even when shooting night landscapes.
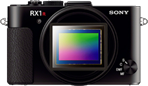
Featuring an optical variable low-pass filter made possible by Sony innovation
We heard that the low-pass filter can be switched on or off electronically. That's an entirely new feature, isn't it?
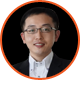
From the outset, the RX1 lens has had extremely high resolving power, and because of this, there were cases of false colour and moiré occurring under certain condition. Because pixel count was increased from 24 megapixels to 42 megapixels in the RX1R II, frequency of false colour and moiré occurrences decreased significantly. However, these phenomena still tend to occur. Consequently, we came to the conclusion that an optical variable low-pass filter allowed users to choose "on" or "off" reduction of false colour and moiré effects depending on their needs.
Since many professionals buy cameras in this class, some users are quite concerned about these occurrences. Typically, changing focus point or angle of view is the only way to solve false colour or moiré when problems occur while shooting photos with fixed camera placement (on a tripod, for example). Now, the camera provides a new function to reduce false colour and moiré as needed without changing focus point or angle of view - by simply using an optical variable low-pass filter.
Here's the reason this function was adopted. R&D had been working on an optical variable low-pass filter as a company challenge, and principle examination of this invention was recently completed. Possibly the best-matched camera model for this technology happened to be the RX1R II. Since the RX1R II goal was "aiming to take the image quality of the ultimate level", we wanted users to enjoy the ultimate sense of resolution while choosing ultimate-level reduction in false colour and moiré. Naturally, we decided to have the new camera feature this new function.

In other words, we didn't plan to add this technology to the RX1R II in the first place, but the technology was close to achievement. Since RX1 and RX1R are sister models, one with a low-pass filter and the other without, this newly developed device enables one camera to deliver the benefits of both models. Because of this newly featured function, we had to painstakingly reexamine designs of other technological elements, but we judged that this was worth trying and our efforts paid off.
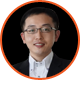
Usually, a general optical low-pass filter is made of ordinary crystal board. However this time, since the filter is electrically driven, software and electronic circuits were newly developed, too. Also, because this device is placed at the center of the camera - behind the lens barrel, in front of the image sensor, and next to the EVF - the device itself has a great impact on its surroundings. It was a painstaking process to adjust RX1 architecture without affecting its compact size, so we worked together with other related developers.
In terms of manufacturing this device, the optical variable low-pass filter has a basic structure consisting of two low-pass filter boards and liquid crystal enclosed between them. Though crystal material is used by regular cameras, enclosing liquid crystal between filter boards was made possible by Sony's proprietary technology, available for the first time in the world. A low-pass filter has a typical property that allows the direction of light to pass straight through or refract depending on polarisation. This polarisation condition can be adjusted by the liquid crystal in the newly developed low-pass filter. Sony has an established record of development and mass-production of variable ND filters, and this new device has inherited the legacy of liquid-crystal-related technology in optical devices for cameras.
On the functional side of the device, this low-pass filter provides a "standard" setting - which took a long time to develop - in addition to "on" and "off" settings. These can be determined mostly by physical maximum and minimum values while we needed to aim for subtle yet perfect balance between resolution feel and occurrences of false colour and moiré. Since crystal has to be driven in a highly precise manner in order to maintain this difficult balance, we discussed this with the image quality group to work out measures for controlling, manufacturing, and determining final tuning. For example, "off" setting may be suitable for natural scenic views (landscapes) and "on" setting may be better for architecture and apparel. However, false colour and moiré cannot be easily identified while shooting. On such occasions, you can choose bracket shooting at three different low-pass filter settings - "on", "off", and "standard" - and enjoy shooting with peace of mind.
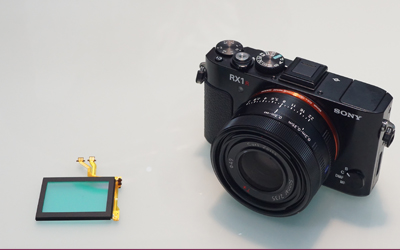
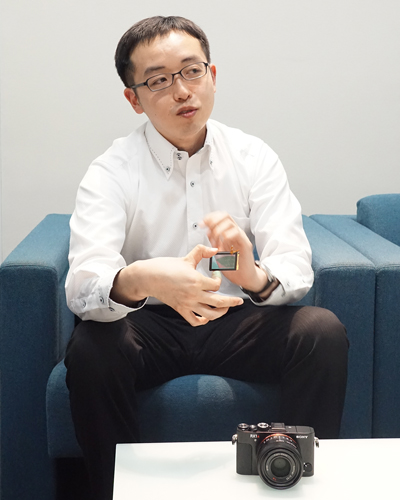
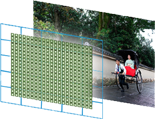
Achieving advanced speed with new feeling through synergy between image-surface phase detection AF and lens-body integrated design
AF is another great evolution achieved through the RX1R II. I guess many users looked forward to this new advantage.
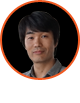
The RX1R II sensor features an image-surface phase detection function that enables prompt focusing on a targeted subject while providing Fast Hybrid AF, which allows high-precision contrast detection. I was in charge of the process of converting detected focusing values into command data for driving the AF system by sending data to the lens unit to move the lens for optimum focusing.
In addition, I was in charge of the AF system during RX1 development, and I realised that AF precision was extremely difficult for a full-frame sensor model, since this required an extremely high-resolution feel and a large-size lens. To obtain satisfying precision, all the team members worked hard until the very last moment of product delivery. I believed the RX1 provided a satisfying level of AF precision, but at that time, there were many ideas that could be reflected in the new RX series and other cameras. Moreover, we already received feedback on AF system response from some customers. Therefore, our development members wanted to improve the speed bit more.
So, we were waiting for this opportunity to put an advanced AF system into the RX1R II. In fact, even before this latest project launch, some team members had already started looking into ways to improve the speed of lens control by making prototypes. Finally, we were able to use this know-how on a real product.
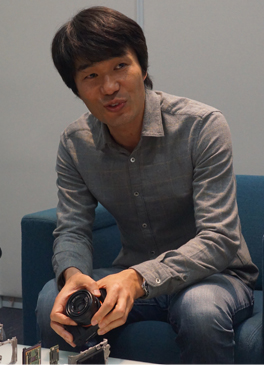

Basic configuration of the motor called an "actuator" embedded within the lens unit has not been changed, but its algorithm was entirely changed. Increased AF speed was achieved through a combination of three technological means - use of an image-surface phase detection system, image sensor and image processing engine renewals, and a newly developed algorithm.
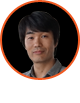
I would say that the AF system was dramatically changed. If you hold the camera and actually use it, you'll experience an entirely different feel in AF behavior. The lens unit contains two lenses for focusing and requires high-precision control. However, due to the increase of pixel count of the RX1R II, these lenses had to be controlled with even higher precision than with the RX1. Moreover, since required lens motion speed was faster and the required precision level was even higher due to new adoption of Fast Hybrid AF, these two lenses required even greater control. When autofocusing finally comes to a stop position, it has to be truly perfect - otherwise, pictures cannot appear crisp and clear from corner to corner.
Because we cannot compromise on this performance, we paid meticulous attention to lens control. Since lens and image sensor are both remarkable, we had to aim for a precision AF system that properly controls the lenses. Although we took advantage of the lens-body integrated design, if we took a wrong direction, the AF precision level wouldn't be sufficiently high or it could generate unwanted operational noise. Therefore, we kept repeating tests with prototype devices to find the best tuning to control lenses in the way best suited to this product while taking into account the target quality level.
Because we can adjust the lens unit as we like on cameras with lens-body integrated design (unlike interchangeable-lens cameras), we can test as many ideas as we can imagine. Since we could put all these ideas into the RX1R II, AF system performance has reached a satisfying level, I believe.

RX1R II also allows users to choose AF-C mode that consistently tracks the motion of a targeted subject.
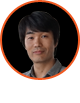
AF-C mode tracks subject motion and keeps on focusing. In the meantime, because the image-surface phase detection sensor can detect subject location, it can avoid unnecessary motion of lenses. The camera features Pupil AF and this can be used simultaneously with AF-C mode. This means the camera can focus on the best spot by tracking the motion of a pupil even if the model moves slightly during portrait shooting. I believe this makes it much easier to shoot good portraits - another example of these advantages.

We've already received positive responses for the much faster AF system, compared with the RX1. In fact, we heard that a customer who uses the RX1 wants to replace it with the RX1R II because of this new AF system. Experienced RX1 users can better understand improvements.
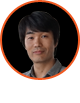
AF system development allows precision lens control that affects the feeling of resolution. So I'd like users to "savour" the taste of this imaging. I was aware that AF control team members were hard at work until the very last stage of development. They continued checking the AF over and over again - even though they made sure that things worked fine - because they were really concerned about quality. We're all satisfied now. But, of course, we have to be skeptical because we're engineers...
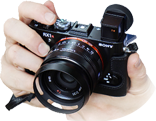
EVF achieves balanced realisation of operability and quality feel, demonstrating the level of "made in Japan" quality control
There are more evolutionary advances, such as a new viewfinder with one-touch popup and retraction design. Could you please tell us about them?

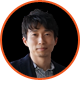
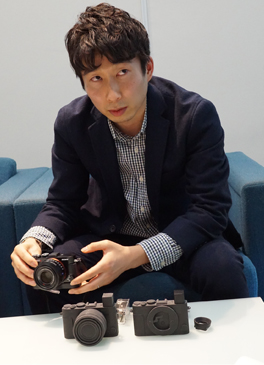

The magnification ratio of the α900 viewfinder was 0.74 and its beautiful images won high praise from users. Partly as a tribute to the α900, the magnification of the RX1R II finder was also set at 0.74. Just as the α900 aimed for the best possible OVF, we aimed for the best possible EVF in the RX1R II.
Regardless of cost, glass lenses with a high refractive index are adopted in all optical elements of the ocular lens. Moreover, two of these elements are molded-glass aspheric lenses to achieve a significant size reduction in the optical-axis direction as well as exhilarating clarity. If you glance through the finder, you'll immediately appreciate this clarity.
While pursuit of higher optical performance was demanding, another tough challenge in the initial stage of design was realisation of one-touch popup action. Sony introduced the first popup-type viewfinder in the RX100 III, but we had to take design to an ideal level when creating the finder for the RX1R II flagship model.
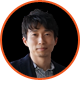
The RX100 III requires two-step action since the eyepiece must be pulled out manually after popping out the viewfinder unit for easy viewing. Retraction of the viewfinder also requires two-step action with the RX100 III. The action of pulling out the eyepiece is also required for the RX1R II viewfinder, but it's designed so the user can complete two actions - popup and pull-out - in one step. This was a significant technical challenge to overcome.
As an early alternative idea, we once proposed a design with one-step action for use of the finder and two-step action for retraction. However, after thinking hard about user convenience, we came to the conclusion that we should provide a viewfinder that only requires one simple push action for retraction.
Nevertheless, we couldn't find any precedent for reference in building this kind of popup finder - not even in other fields than camera mechanisms. But the funny thing is that Sony's mechanism design developers feel higher motivation to create something that never existed before.
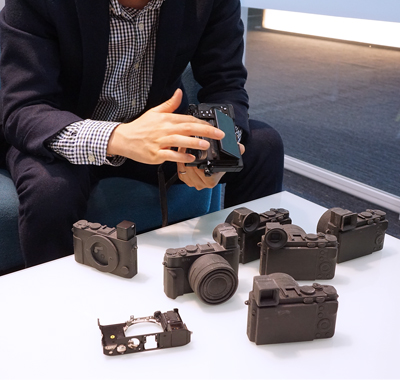
Designers came up with various ideas and made numerous prototypes, including multiple mechanism concepts to allow one-step action. However, if the popup lever and other parts looked unattractive, we turned them down as unsuitable to the quality level of the RX1 series, Eventually, we determined to use one mechanism, taking into account various factors - operability, quality feeling, strength/durability, etc.
The chosen mechanism works in this way. A lever-type metallic arm slides up and down along a rail and starts the pulling action at the near end of the rail where the track course changes. With this mechanism, a downward push on the finder unit causes the metallic arm to start pulling the eyepiece inward to retract the unit through one-step action.
After we decided on the basic structure, the next hurdle was the quality feeling of popup action. While it's easy to pop up the unit with spring force, this created a loud popping noise. To realise high-quality motion suitable to the RX1, we added a damper to deliberately slow the popup speed. However, if we slowed this too much, it could delay quick shooting ability and diminish the user's desire to immediately look in the finder. Therefore, we needed to tune the mechanism to maintain the speed at a level that was neither too fast nor too slow.
If you hear the word "damper", you may think of automotive terminology. In fact, we did some research in dampers that are used as interior parts and in the instrument panel of luxury vehicles.
Then, we encountered another hurdle - creating a quality feeling when pushing in the finder unit. We pursued this feeling throughout a series of actions, including the "click" sound as the viewfinder locks in place inside the camera body. To tell the truth, when the order came from product planning, we never thought we could achieve this high level of quality. We had to realise an ideal balance between finder performance and one-step action and take this quality feeling to the max while allowing consistent mass-production. These challenges caused us considerable stress.
However, we remained confident that we would ultimately fulfil all requirements. And, we received constant support from Sony's related departments, factories, and parts manufacturers in pursuit of this quality feeling to the very end of the development process. As a result, we could satisfy the goal and deliver the best popup viewfinder ever. I look back over the whole process with great appreciation.

There's one more thing to note regarding the EVF. Because it looked so remarkable, we felt we should provide an eyepiece cup - even as an attachment - for those who always use it. So after the camera development, we designed the eyepiece for the market, as a supplied accessory for the camera package.
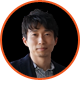
We repeatedly discussed what kind of shape would be suited to the camera without diminishing the sense of quality. After repeated trial and error to provide beautiful styling without accidental detachment while the camera was in use, we came to the conclusion that the cup should be attached with a small knob, shaped like the winding device of a watch. The eyepiece cup itself was thoroughly analysed, and although we considered the possibility of a square shape, we determined on a round shape for easy viewing and comfortable fit while allowing use in either horizontal or vertical camera orientation.

Another characteristic feature is the tilt-type LCD monitor. This design was realised after a number of discussions and tests of how to enhance operability while maintaining the original quality feeling.
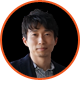
We determined to use magnesium alloy for this tilt-type LCD monitor because a plastic frame doesn't have a sufficient feeling of solidity and high quality for RX1 design. When you push the tilt-type LCD back into the body, it returns to place neatly, thanks to an enclosed magnet. Moreover, the appearance of the back side of the body is important, since it's visible when the LCD panel is in tilted position. So we made a painstaking effort there. I believe this detailed design gives the RX1R II a rare sense of quality — which stands out among compact cameras, including those of other manufacturers.

It took more than a half year to complete the whole design. We produced a number of mock-up models for repeated discussions.
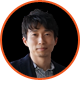
The overall silhouette of the RX1R II is almost the same as the RX1, but placement of the lens was shifted slightly toward the grip to make space for the popup-type viewfinder. Due to this minor change in lens placement, we reviewed these mock-ups for optimal layout of other elements, such as dials, hot shoe, tripod socket, grip shape, etc., in order to maintain user operability. Although the external design looks almost the same as the first-generation RX1, the internal design was created from scratch, once again. In terms of materials, we conducted repeated simulations of strength analyses and adopted high-functionality reinforced engineering plastic for the popup mechanism to achieve strength and durability suitable to this RX1 viewfinder.

One unique aspect of the RX1R II is its detailed design. We pay meticulous attention to every small part, use of materials, and quality feel. Quality control is also thoroughly pursued. All RX1 products are built in Japan, using a "clean booth" system throughout the entire production line, from manufacturing of lens elements and image sensor to assembly of lens and body.
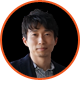
We adhere to details like physical clearance between external parts. For example, if there's no clearance gap between the body and the viewfinder, the finder unit doesn't pop up properly due to friction. If there's too big a gap between them, the quality feel cannot be maintained. In order to obtain consistent minimal clearance, builders manually assemble parts through careful one-by-one adjustment at our factory in Japan. This level of adjustment is uncommon for regular cameras, I believe. Engraved marks like the Sony logo are handled on a one-by-one basis by our manufacturing factory in cooperation with parts makers. Furthermore, "MADE IN JAPAN" is engraved on the bottom of the product. I believe this camera represents a true crystallisation of Japanese technologies, reflecting pride of craftsmanship.

Holding. Shooting. Viewing. Satisfaction in all phases of operation. The best quality available anytime, anywhere
Please send a special message to potential RX1R II users.
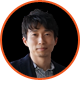
Most people can't imagine that a camera with this small size chassis contains a full-size image senor and α900-class viewfinder. It's unthinkable! Yet this is a camera you can casually slip into your bag or hang around your neck on a strap. Why don't you treat it like a carefree compact? Bring it along to all the places you used to take the trouble to carry your bigger camera. I'd like you to enjoy the freedom of "carrying the best quality anywhere, anytime."
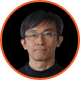
I'd like you to carry it and shoot photos every day. This camera allows you to shoot natural images of daily life rather than artificial photos. You can capture images faithfully of what you actually see. Rather than crafting sharp pictures artificially, the camera delivers images with natural frequency characteristics. That's how the camera is built and what we aimed for. And since it's so compact, I'd like you to use it all the time.
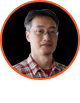
I climb mountains sometimes and carry the RX1R II with me, but I never have trouble because of the compact design. I shoot landscape shots, and since this camera depicts very small details, it captures extremely refined images with a sophisticated finish. In other words, it allows you to get the image quality of medium format cameras, with the best possible quality performance in such a compact body. Please carry it around and really enjoy photography.
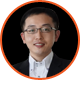
The optical variable low-pass filter feature is a world's first invention, symbolising Sony innovation. I'll be happy if customers feel exhilarated and sense its premium feeling as they touch this RX1R II.
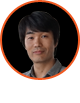
You can carry it every day and shoot photos with ease like casual snapshots. As you hold and aim through the camera, it accurately focuses on a subject, allowing you to shoot immediately. Since it features Pupil AF, the camera is also suited to taking photos of children because the 35mm lens is easy to handle and allows you to shoot from optimal distances. I recommend you carry this camera when taking walks with your family. It definitely lets you catch a child's most appealing expressions. Of course, you can use this camera in a wide range of situations including landscape shots as well as snapshots and portraits. It also allows users who take pictures of various subjects to enjoy photography every time it's used. And, it even provides Fast Hybrid AF for movies. Please try movie shooting, too.

RX1R II design and manufacturing have taken a great amount of time and effort, not only by designers but also by manufacturing staff. Each one of these cameras is produced with scrupulous effort by Sony staff alone. Since we've paid great attention to the quality feeling, we'd like you to "savour" this quality for yourself as you hold it. We hope you'll enjoy photo shooting using both viewfinder and LCD monitor. And on top of these, I truly want you to experience the post-shooting enjoyment of the high precision feeling and natural depiction of the photos. We've made the most of all details, so the camera can give you maximum satisfaction in all aspects of taking pictures. We truly hope you'll enjoy the RX1R II to the fullest extent possible.